Wood-Be Weight Savior – Technologue
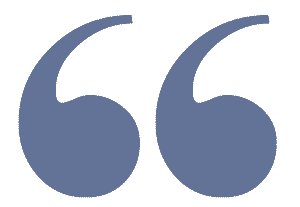
The next big light/strong material grows on trees
Stop the 40-ton presses and cool the autoclaves. There’s a new light/strong/cheap material poised to join the vehicle engineering toolbox, and it’d be recognizable to the designers of Conestoga wagons. Forget titanium, carbon fiber, and high-strength steel. The hot new substance on the automotive scene is … wood?
Yes, wood might no longer be just for dashboards and Morgan body framing. Researchers at the University of Maryland have developed a way to make cheap, renewable, fast-growing, CO 2 -consuming wood 10 times stronger and tougher than natural wood, aligning its strength with some steels but at one-sixth the weight and vastly lower cost. (The cost savings over carbon fiber apply, as well.)
It’s called “densified wood.” Producing it involves boiling the wood in a solution containing sodium hydroxide and sodium sulfate just long enough to remove 12 percent of the cellulose, 73 percent of the hemicellulose, and 46 percent of the lignin. It’s then boiled in deionized water to remove these chemicals and then hot-pressed (perpendicular to the growth direction) at 725 psi and 212 degrees F until it’s squashed to about 20 percent of its original thickness.
Removing lignin and hemicellulose leaves the wood cell walls porous—so the hot press completely collapses the tubes used to transport water and nutrients throughout the living tree. The remaining cellulose nanofibers remain highly aligned but are much more densely packed. When they’re packed that closely, the hydrogen atoms in their hydroxyl groups are close enough to “hold hands,” making it way harder to push, pull, or tear them apart.
How much harder? After pressure-cooking, the specific tensile strength (how much force per area you can apply to the wood before it breaks, divided by its density) roughly quadruples. That makes it stronger than steel and aluminum—it’s even about one and a half times better than a lightweight titanium alloy (TiAl 4 V). Compress it along the growth direction, and it’s 5.5 times stronger than undensified wood and slightly ahead of mild steel.
Surprisingly, the densified wood also becomes tougher—harder to scratch or fracture via impact. Often, improving a material’s strength makes it more brittle. But in this case that hydrogen hand-holding also makes the treated wood 10 times stiffer and harder to break than natural wood, and its scratch-resistance improves 30-fold. Painting makes it immune to the effects of humidity.
University of Maryland researcher Liangbing Hu says the material can be joined mechanically via rivets or bolts and/or bonded with adhesives. He claims that the surface finish and hardness coming out of the press are sufficient to accept a class-A painted finish, so it could form exterior panels as well as structure. And with no exotic resins it’s easier to recycle than most composites.
There are some caveats and asterisks, of course. Metals can be cast or stamped to nearly any shape imaginable, but densified wood’s strength aligns with the original branches and trunks. So although it can be bent quite a lot, laminated, and formed as tubes and other shapes during the boiling/pressing process, there will be geometric limitations. And although Hu’s team forecasts that densified wood will be cheaper than carbon fiber, at this point the cycle time to produce parts is considerably longer, making it suitable only for low-volume applications. A good one: bulletproofing. Laminating several thin sheets of densified wood with their growth directions oriented at 90-degree angles shows promise as a lightweight, thin, cost-effective armor plating capable of resisting at least small arms fire.
If this isn’t interesting enough, the Maryland team has other automotive wood tricks: Removing the lignin from wood and infusing it with methyl methacrylate produces transparent wood that’s stronger and better insulating than glass. A biodegradable nanocellulose paper could replace plastic on instrument lenses, and a photonic paper is showing promise in advanced battery applications. We suggest UMD and Hu produce an all-wood concept car to showcase these technologies. Perhaps Automobile design editor Robert Cumberford could style it as a follow-up to his 1982 wood-bodied Martinique.
Woodies are back!
And women around the world rejoice!
......... ummmmmmm......
Please don't incite my juvenile sense of humor, Bob, and whatever you do, don't say anything about Pandora's box!
My goodness, one can grow a car in their backyard.
Interesting to read this and the application. I wonder how far this will get in any real application.
I’d like to see a picture of some finished product. I’m assuming it doesn’t actually look like wood. I imagine the grain is gone, or at least significantly disturbed. Very interesting topic though.
There’s a picture in the OA, just a panel, without explanation, but I assume it's what comes from the process. There's a definite grain.
Sounds a little like how rayon is made